自社開発IoTで生産性が向上したら、働き方改革も実現されていた
自動車部品製造の旭鉄工は、自社開発のIoTを使用した「製造ライン遠隔モニタリングシステム」の導入で、工場の劇的な生産性向上を実現。改善の見える化による従業員のモチベーションアップと、残業時間の大幅な短縮にも成功している。
文/狐塚淳
トヨタ生産方式と中小企業
愛知県碧南市に本社を置く旭鉄工は、従業員数約450人の自動車部品製造の会社だが、自社開発のIoTで生産性向上を成し遂げたことで注目されている。同社の木村哲也代表取締役社長が、21年間務めたトヨタ自動車から転籍してきた2013年から、現在の生産性改善の取り組みが始まり、2015年初頭には、自社開発のIoTを使用した「製造ライン遠隔モニタリングシステム」(以下iXacs)を作り上げた。
旭鉄工はトヨタの一次仕入先で、従来から工場ではトヨタ生産方式を導入し、生産の効率化を目指してきた。トヨタ生産方式に基づいた改善は生産数、停止時間、サイクルタイムを継続して測定し、その数値をもとに共有・実行・目標設定という生産改善のサイクルを回していく。しかし、中小企業の現場では、この最初の測定と記録が大きな負担になる。専任の測定者を置くことは難しいから、生産の合間に測定・記録を行うため、測定タイミングのずれや測定漏れが発生しやすい。また、人手による測定では停止秒数などが不正確になりがちで、不正確なデータからは原因がうまく究明されないケースもある。
この作業にIoTを活用できないかと木村氏は考えた。
「不良品の発生率が高いような現場の場合、もっと別のアプローチもあったかもしれませんが、工程内の不良は0.2%以下で、不良の多くは箱詰めの際の傷でした。これはIoTでは削減できません。改善、効率化が望めるポイントを見定めてのIoT化に取り組みました」と、木村氏は振り返る。
木村哲也代表取締役社長
自社開発IoTが生まれた理由
トヨタ生産方式の「時間は動作の影」という考えに基づき、1つの生産ラインで1個の部品が生産される時間(生産ピッチ)をリアルタイムに監視し生産数を記録し、所定の時間が経過しても部品が生産されない場合には設備停止と判定し、次の部品生産が行われるまでを停止時間としてカウントするロジックを考案した。
(生産数)=((稼働時間)-(停止時間の合計))/(サイクルタイム)
という式が成立する。生産数を増やすには停止時間を減らすか、サイクルタイムを短くすることだ。そのためには1個の生産が終了したタイミングを正確に計測し続ければいい。しかし、生産ラインにIoTベンダーのソリューションを導入しようとすれば数百万から1千万円単位の投資が必要になる。
中小企業ではコストが高ければ各ラインにIoTベンダーのソリューションを導入する投資は難しいし、昭和から使い続けている設備の場合、IoTセンサーなどを機器に組み込むことが難しいケースもある。そこで、旭鉄工では、秋葉原で購入可能な小型コンピュータ(RaspberryPi)と安価な光センサー、リードスイッチなどを組合せ、設備の外側に装着可能なIoTシステムを自作し、測定を可能にした。
部品が生産されたことをリードスイッチで磁気的または光センサーで光学的に確認してパルスを発生させ、送信機から受信機に無線で飛ばす。パルスの時間間隔が閾値内であるかどうかを判定し、閾値より長ければ停止状態と判定、ビジュアル化して従業員のスマートフォンなどにクラウド経由で配信して、生産個数、停止や遅れの情報を共有する。
iXacsを外付けで導入しているライン
トヨタ生産方式では通常壁面に「あんどん」と呼ばれる大型ディスプレイを設置してこれらの情報を表示・共有しているのだが、「あんどん」は高価なうえに工場のレイアウトなどによっては生産の手を止めないと見づらいケースもある。誰もがスマホを持っている現代では、iXacsのやり方の方が簡単に確認できる。
測定結果がリアルタイムで得られるようになり、旭鉄工では停止や遅延などを改善するためのミーティングを翌日に行う形にした。これによって、記憶が薄れることもなくスムーズな分析が可能で、改善活動にもすぐに着手できるため、現状把握から検討、改善までの工程の短縮が可能になった。停止時間の改善については停止時間の長かった要因から先に取り組み、サイクルタイムの短縮は加工に関係のない部分から取り組んだ。
「現在、旭鉄工で常時生産しているのは250ラインです。その6割の150ラインでモニタリングをしているのですが、そのうちの100ラインは特に大幅な生産性の改善が見られます。この100ラインの平均では、43%という大幅な改善効果が表れています」(木村氏)
サイクルタイムについても、34個のアイテムでサイクルタイムが15.4秒から11.7秒に短縮されるとともに46個のアイテムで停止の割合が33%から5%に減り、初期は1時間160個だった生産量が1時間287個に上昇したなどの実績がある。これを設備の増設で補おうとすると4,545万円が必要となり、その分のコストが削減された計算になる。
「停止時間の改善もそうですが、サイクルタイムの短縮も生産量を上げるには効果的ですが、意外と取り組む企業は少ないです」と、木村氏は自社実績をもとに説明する。
IoTにより、人手を代替するというアプローチ
IoTというと、人間が正確に感じることのできない振動などの情報をセンサーでデータ化し、それを分析して、従来は不可能だった予知保全などを実現することに関心が集まりがちだが、旭鉄工のIoT利用へのアプローチは全く異なる。
人が手作業で行っていたデータ収集をセンサーに代替することで、より精密で正確な観測が可能になり、その観測データを無線で飛ばし記録を自動作成することで、人の記帳よりも何倍も早く、タイムラグなしにビジュアル化されたデータを分析し、解決策を検討・実施できるようになる。つまり、人手の代替と課題発見・解決のスピードアップを目的としたIoT活用だ。
考え方としてはシンプルだが、設計・導入も容易だし、成果も確かめやすい。
部品製造では、決められた納期までに必要な数の部品を作らなければならない。間に合わないなら操業時間を延長するか、新たに設備を購入して製造ラインを増やす必要があるが、それでは労務費や設備投資が増大する。そこで、現行のラインの課題を発見し、改善することが必要になるが、iXacsなら、この改善を大幅にスピードアップすることが可能だ。
IoT以外にも、旭鉄工ではスマートスピーカーによる生産性向上に取り組んでいる。設備間で材料の受け渡しなどを行う際に、手を放すことなく蓋の開閉など作業の記録をスマートスピーカーに話しかけることで行わせている。人の動きに注目して効率化を図るという点は共通している。
スマートスピーカーも生産性向上に一役買っている
生産性が向上したら、働き方が変わった
こうした取り組みの結果、同社ではIoTを導入した2015年~2019年で月間の労務費が2千万円ずつ下がり、年間2億円の節減を達成している。労務費が減るということは、必要な生産量を達成するために残業に頼らなくて済むということだ。
同社の社員の一人は「2013年以前は土曜出勤が普通でしたが、最近は休日出勤はほとんどなく、月の残業時間は2~3時間です」と語っていた。
残業時間の削減から「働き方改革」に取り組んだ会社の多くが、そこから生産性向上へ向けての舵取りに苦しんでいるが、本来は旭鉄工のように生産性向上を実現し、結果として残業時間削減が達成されるのが望ましいのはもちろんだろう。
そして、IoTによって改善が見える化することで、従業員のモチベーションがアップすると木村氏は指摘する。
「0.1秒単位の改善でも目に見えるようになったことで、さらなる改善を達成しようと頑張るようになります。自分たちの達成したことを数値で確認できることで、さらなる改善目標も数値として認識でき、モチベーションが高まります」
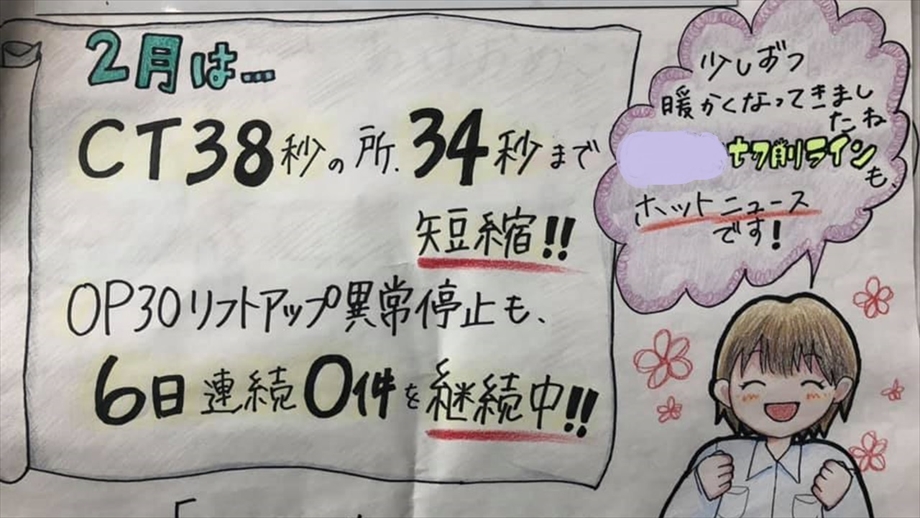
従業員が自主的に作成し掲示したイラスト。改善の見える化でモチベーションが高まる
そのためには導入時に注意しなくてはならない点があるという。
「IoT導入で、新しい作業が加わるのでは、従業員に定着しません。これまで必要だった作業の一部を、より楽により便利にシステムが代替してくれる形にしなくてはなりません。メリットがあれば現場はやってくれます」(木村氏)
同社では生産現場だけではなく、事務系の部署でもメールをSlackに置き換えるなど、生産性の改善を進めている。来春からは働き方改革関連法の施行がさらに進み、すでに残業減や休日日数増を成し遂げている企業にもより厳しい基準が求められるが、木村氏は「法律は守らなければなりませんし、まだまだ工夫の余地はあると思います」と自信を見せる。
見える化したデータでさらなる事業展開へ
自社の成果を元に、木村氏は2016年9月に旭鉄工の敷地内に別会社iSmart Technologies(iSTC)を設立し、自社開発のiXacsをサービスとして他社に提供開始した。同サービスの特徴は、ユーザーの設備を選ばずに、1ライン分のソフト使用料が月額300円からという低コストで導入が可能なことで、すでに約200社で導入実績があり、そのうち80%を中小企業が占めている。また、iSTCではデータ分析のアドバイスやeラーニングによる改善力向上サービスなども提供し、生産性向上をサポートしている。
同システムは「第7回モノづくり日本大賞特別賞」など、多くの賞を受賞している。ユーザーの導入成果は200ラインをピックアップして計測した数字では導入から5か月で平均1.25倍の生産性向上になっている。
旭鉄工では、自社のタイ工場でもこのシステムを使って、現地の生産性改善に実績を上げている。海外拠点の管理にも効果は実証済みだ。
iXacsを説明するための模型。一目で仕組みを理解してもらえるという
同社では、設備稼働データを蓄積しており、今後はこのデータをベースに金融関係企業と連携した事業にも乗り出していく考えだ。現在は事業性評価などへの利用で保険会社との提携を進めており、銀行との協力も模索していくという。
「現在は100社のリアルタイムの生産データが蓄積され続けています。これが1,000社に増えれば、財務短信などと比べ、リアルタイム性の高い社会の景況感も見えてくるでしょう」と、木村氏は今後を展望する。
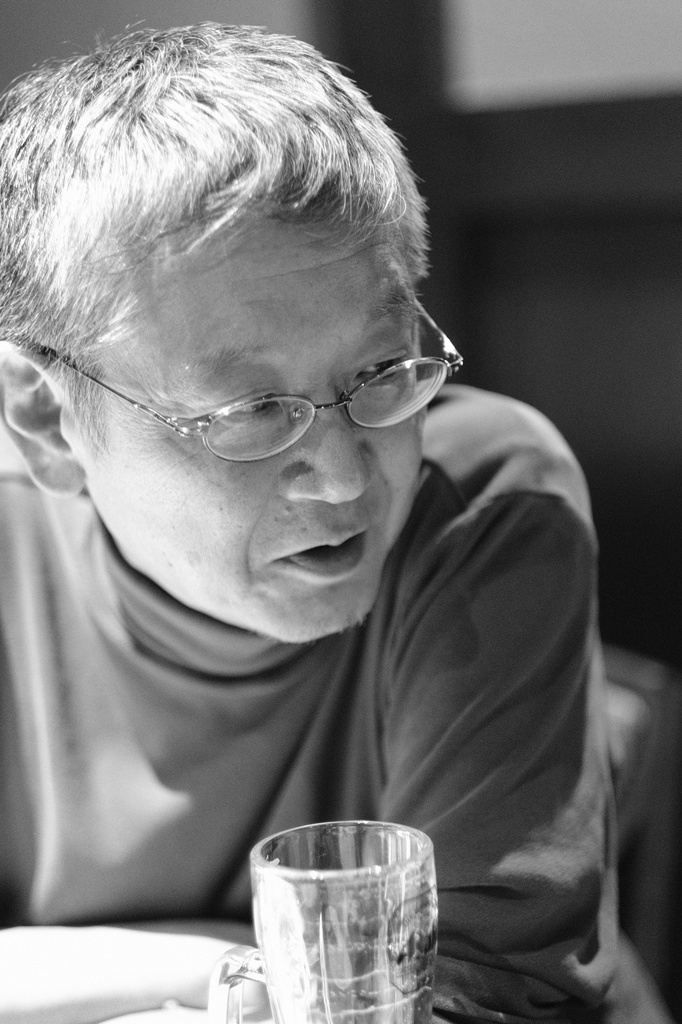
筆者プロフィール:狐塚淳
スマートワーク総研編集長。コンピュータ系出版社の雑誌・書籍編集長を経て、フリーランスに。インプレス等の雑誌記事を執筆しながら、キャリア系の週刊メールマガジン編集、外資ベンダーのプレスリリース作成、ホワイトペーパーやオウンドメディアなど幅広くICT系のコンテンツ作成に携わる。現在の中心テーマは、スマートワーク、AI、ロボティクス、IoT、クラウド、データセンターなど。