フロントラインワーカーをネットワークにつなげて
IoTやAIなどデータ活用の成果を最大限に引き出す
TACTICS-2
日本マイクロソフトは産業を横断的に担当したエンタープライズ事業本部を昨年10月に改組し、製造業と非製造業の二つに分割した。製造業専任となるのがエンタープライズ製造事業本部だ。そして今年3月15日、国内の製造業に向けた日本マイクロソフトの取り組みを発表し、事業を強化することを印象付けた。同社は製造業を横断的に支援する体制を整えて、国内製造業のデジタル化を支援していく。ここでは具体的にどのように支援するのか、どのような成果が出ているのかをリポートする。
ようやく動き出したデジタル化
本格的な取り組みはこれから
日本マイクロソフトのエンタープライズ製造事業本部では素材・化学から設備・装置、部品、そして自動車、電子機器、電機などの完成品まで、製造業全体を一貫して営業および支援する体制を構築している。さらに製造業を支える電力・エネルギーも網羅する。
この体制によって国内製造業のデジタル化を製品やサービスだけではなく、ビジネス構築や人材のスキルアップから支援する。そのアプローチは次の三つだ。まずデジタル・フィードバック・ループ構築支援により、個別最適化されたシステムからデータを解放し、レジリエントな意思決定に必要となる自由自在なデータ活用環境を実現する。具体的には各種データ活用およびAI活用のワークショップ、Azureデータプラットフォーム、Azure IoT&AIプラットフォームなどを提供する。
二つ目は新しい製品・サービスのアジャイル開発支援により、製造業のフィジカルとマイクロソフトのデジタルを組み合わせた開発でディスラプター、すなわち欧米や中国などの競合に対抗する。具体的には戦略的パートナーシップに基づくアジャイル開発手法と必要なリソース、Azure DevOpsなどを提供する。
そして三つ目は従業員のデジタル武装およびDXスキル獲得を支援することで、現場の従業員を含めた人材のデジタル人財化を図り、オペレーションの現場からイノベーションを創出する。これにはローコード開発基盤となるPower Platformや、ワークショップ、ハッカソン、トレーニングプログラムなどが提供される。
国内の製造業はデジタル化において世界をけん引する状況にはない。しかしコロナ禍を経験し、日本の製造業においてもデジタル化への考えが本格化しつつあり、推進体制を整える企業も増えているという。ただし積極的なデジタル化への検討が進んでいる一方で、具体的な取り組みが本格化している段階には至っておらず、PoC(概念実証)が動き出したという状況が今である。
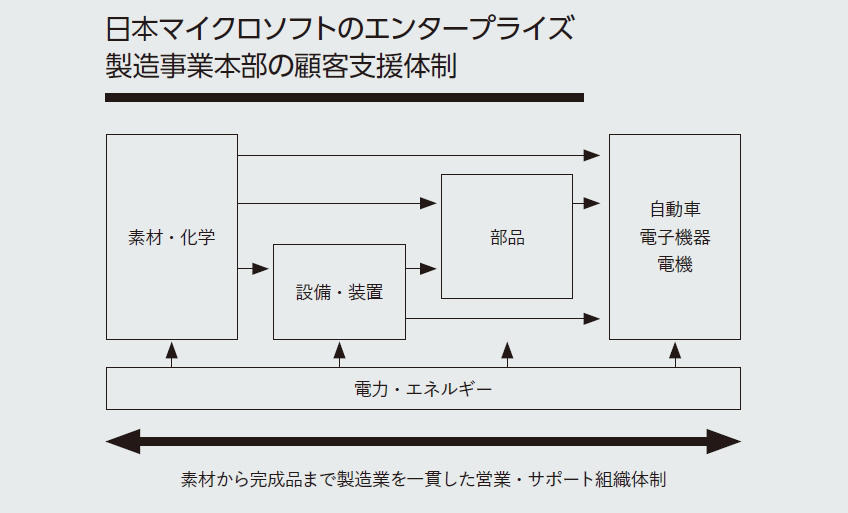
取り組みを具体化させるシナリオ
現場で働く人の働き方改革から
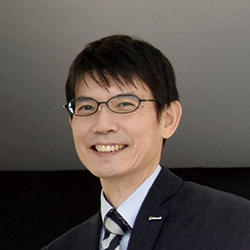
エンタープライズ製造事業本部
製造インダストリー・アドバイザー
鈴木靖隆 氏
ようやく動き出した国内の製造業のデジタル化への取り組みを本格化させるには、どのようなシナリオが効果的なのだろうか。日本マイクロソフトでは国内製造業向けにフォーカスするデジタル化のシナリオについて七つの領域で五つの中核となるシナリオを提示している。
まず従業員の働き方改革だ。オフィスワーカーのリモートワークは定着し、進展を続けているが、製造業においては工場や倉庫、作業現場で働くフロントラインワーカーの生産性と安全性の向上が重要となる。日本マイクロソフトでは実際にデジタル化に積極的な製造業からの引き合いが非常に多いという。
日本マイクロソフトの顧客の事例では、タイの工場で新しいラインを立ち上げる際に、コロナ禍で出張できないため同社のMRヘッドセットのホロレンズを活用してリモートのコミュニケーションでラインを立ち上げた。この事例は製造業の現場での技術伝承などにも応用できるだろう。
日本マイクロソフトのエンタープライズ製造事業本部で製造インダストリー・アドバイザーを務める鈴木靖隆氏は「製造業の従業員の半分はフロントラインワーカーです。オフィスワーカーはMicrosoft 365やTeamsを業務に活用していますが、フロントラインワーカーは使っていません。そもそも1人に1台のデバイスもありません。フロントラインワーカーの生産性や安全性の向上には情報を利用したりコミュニケーションしたりするためのデバイスが必要です。デバイスがなければIoTやAI、エッジコンピューティング、クラウドなどのテクノロジーを活用した恩恵を受けられません」と指摘する。
ネットワーク環境が決して良好ではない工場や倉庫、作業現場でデバイスをどのようにネットワークに接続するのか、現場で作業をする人たちに適したデバイスとは何かなど検討の余地はあるが、市場にはさまざまなデバイスが流通しており、ネットワーク接続に関しても解決策はある。
鈴木氏は「例えば工場では消費者の多様かつ激しい嗜好の変化に応じて少量多品種の製品を、頻繁に製品を変更しながら生産しています。また昨今ではコロナ禍や地政学的リスクにより部材が調達できないなど、ラインを頻繁に組み替えて対応しています。こうした対応を人手で行うのは非常に時間がかかりますし、多くの人手を必要とします。少ない人数でリアルタイムに近い形で製造の現場をコントロールするには、人と機械がネットワークにつながる必要があります。すでに機械をネットワークにつなげている企業はあります。しかし人がつながっていないのです」と指摘し、「機械と人の両面でプラットフォームを提供できるのはマイクロソフトだけだと自負しています」とアピールする。
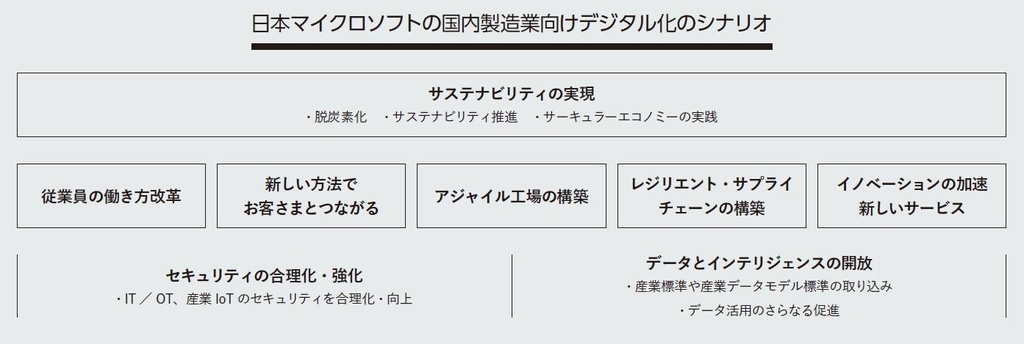
サプライチェーン全体の効率化に
データ交換のための標準化が必要
日本マイクロソフトが提示する国内製造業向けにフォーカスするデジタル化のシナリオの二つ目は、デジタルの力を生かしたカスタマータッチポイントの強化だ。これはデジタルセリング、デジタルマーケティングなどの支援となる。
三つ目は工場オペレーションの高度化や設備効率の向上、技術伝承の促進などを目的としたアジャイル工場の構築だ。ここではIoTやAI、デジタルツインなどのテクノロジーを活用した支援が行われる。四つ目のレジリエント・サプライチェーンの構築では、コロナ禍や世界情勢などによる部材不足など、予測できない変化を前提としたサプライチェーンの運用を支援する。五つ目は製品やサービスの開発・設計をより効率良く、より短いリードタイムで行うための支援だ。
これら五つの中核領域に加えて基礎となるセキュリティの強化やデータや知見を相互に活用できる環境の整備、そしてデジタル化に並ぶ製造業の経営課題であるESGやSDGsなどへの取り組みなどサスティナビリティの実現についても支援する。
鈴木氏は「クラウド、データプラットフォーム、IoT、AIなど、特定のソリューションを提供できるベンダーは多くありますが、マイクロソフトはこれらの全てを提供できる上に、Microsoft 365やDynamics 365、Power Platformなどワークフォースの領域も提供しています」と強調する。
製造業に限った話ではないが、サプライチェーン上で展開されるビジネスをデジタル化する場合、取引先のデジタル化が遅れていると自社が投資したデジタル化の効果が十分に発揮できないという問題が想定される。
あるメーカーでは自社で構築したIoTシステムを取引先に提供して導入してもらうことで、取引先の作業工程のボトルネックの特定と解消に成功したという。メーカーがサプライチェーン上の取引先に仕組みを提供して効果を最大化する、あるいは取引先とシステムを連携させて効率化を図る、さらに自社および自社グループの複数の生産拠点のシステムを連携させてオペレーションを一元化するといった場合、障壁となるのがデータの形式だ。
鈴木氏は「データ交換のための標準化が非常に難しい。現在、日本を代表する業界団体とどのような活動ができるのかを検討するなど、データの標準化に向けた方策を探っています」と説明する。
具体的なユースケースで提案
コマツ産機の予知保全システム
日本マイクロソフトが提示する国内製造業に向けたデジタル化の五つのシナリオにおいて、実際にどのような営業活動をすれば良いのだろうか。鈴木氏は「技術や機能の紹介では共感を得ることは難しいでしょう。なぜなら国内製造業の多くのお客さまはデジタル化に関して経験をしたことがないシーンが多く、想像ができないからです。お客さまに具体的なユースケースを示して説明すると、納得してもらえます。今後は五つのシナリオに対してそれぞれ具体的なユースケースを幅広く用意して、お客さまへの提案の内容を拡大していきたいと考えています」と話す。
同社が行っている国内製造業への支援について最新のユースケースをいくつか紹介する。まずコマツ産機のAzure Machine Learningを活用した生産設備の予知保全システムから見ていこう。同社はコマツグループでプレス機械や板金機械の開発、製造、販売を事業とする会社だ。
製造業の生産現場では設備の部品故障によるライン停止が大きな損失につながる。そのため小まめに点検して定期的に部品を交換する定期保全が一般的になっている。しかし定期保全は保全コストの最適化が難しいため、故障を予知してあらかじめ対策する予知保全が望まれる。
予知保全には設備に各種センサーを取り付けて状態監視を行う手法がある。しかしセンサーが壊れる、保守データの管理が難しいという問題により状態監視が機能しなくなるケースがある。そこでコマツ産機は稼働管理システム「産機Komtrax」のデータと機械学習およびAIを組み合わせて予知保全を行っている。
産機Komtraxは機械に取り付けた通信端末から稼働情報をクラウドに送信して蓄積し、管理者はどこからでも機械の状態を自分の管理点に合わせて確認できるシステムだ。この仕組みとAzure Machine Learningを組み合わせて予知保全システムを構築した。
例えば同社の大型サーボプレス機を導入しているトヨタ自動車で次のような取り組みを実施した。大型サーボプレス機に搭載されるサーボダイクッション装置の大型ボールスクリューと軸受けの摩耗や劣化が「ドカ停」と呼ばれる長時間停止につながりやすい。
そこで産機Komtraxを利用して個々の機械からデータをクラウドに収集し、さらにトヨタ自動車のモーターの振動測定による予兆検知方法の情報をセンサーの信号と突き合わせてAIで判定することで予知保全を行う。
高価な機械学習ツールと比較して正答率が同等の結果が得られるAzure Machine Learningにコスト面で圧倒的なメリットがあったこと、機械学習のモデル構築にMachine Learning デザイナーを使うことで、AIの専門知識や高度なプログラミング技術がなくてもノーコードで正答率の高いモデルを作ることができたことなどが評価された。
この仕組みは劣化部位の特定にも応用された。プレス機械の主要駆動部はモーター、ベルト、減速機などがあり、これらは機械的に結合されている。そのため取得データの解析波形には各種の劣化情報が含まれていると仮説を立てた。この解析波形をAIにかけることで劣化部位が特定できると考え、Azure Machine Learningでトライアルした。
産機Komtraxの稼働掲示板に劣化バロメーターを追加し、機械の劣化状態を色で表示する。機械を選択すると残存寿命グラフが表示されるとともに、交換計画リストにAIで判定した劣化部位が表示され、的確な保全計画が立てられる。
残存寿命グラフではプレス機の各駆動軸の残存寿命の推移を時系列で表示し、残存寿命が下がるとグラフが低い位置に表示される。グラフにカーソルを合わせるとその日の値が確認できるのだが、これはPower BIのレポート機能で実現した。
また残存寿命の低下を検知したら登録されたメールアドレスにアラートを送信する機能は、条件設定するだけで機能するAzure上のロジックアプリを利用し、専用のメールサーバーを用意しなくてもMicrosoft 365のOutlookで実現できた。
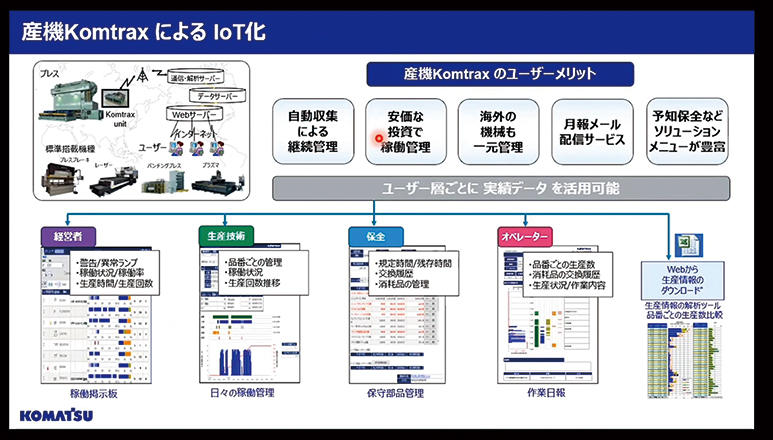
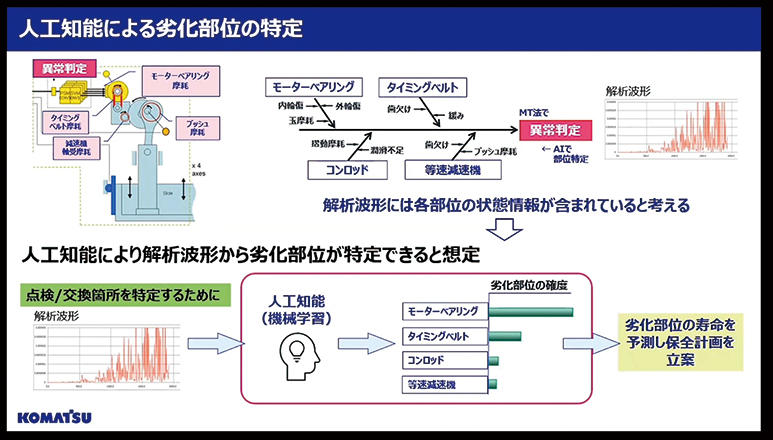
リコーのデータ基盤の利活用
旭化成のデジタル人勢育成
リコーでは顧客に対して製品の品質やサービスの向上に向けて、工場で生み出される各種データや、顧客の職場でのリコー製品の利活用の結果から得られるデータの活用に取り組んでいる。この取り組みを支える製品ライフサイクル全体のデータ基盤をAzure Synapse Analyticsで構築した。
例えば工場では製品情報や工程品質の正偽情報を集めて分析し、AIを利用することで今まで生じたことについてフィードバックで制御するという手法から、起こることを予測してフィードフォワードで制御する手法へと進展させられる。品質の安定化やプロセス制御の自動化にもつなげることができる。
リコーには市場で稼働している数百万台のMFP(複合機)やプリンターがある。市場では1台ごとの稼働データに基づいた顧客サービスやメンテナンスが行われているが、それらの稼働データもAzure Synapse Analyticsで構築したデータ基盤に収集して利活用することで、次機種の開発設計の品質、開発スピードアップにつなげられる。
同社ではこれまでもこれらのデータを蓄積してきたがデータ量が膨大であり、データがカタログ化されておらず利用しづらかったことなどが要因で十分利活用できていなかった。
データ基盤を利用する社員とデータが増えており、データの相互利用も始まっている。データの増加についてはデータカタログの整備が必要となっており、Azure PurviewのPoCを実施している最中だ。ものづくり以外の領域に広げることで、例えば社内での業務改革をデータに基づいて効果的に進めることもできる。
旭化成ではAzureの複数のサービスを利用してデータマネジメント基盤「Data Exploration&Exchange Pipeline(DEEP)」を構築した。グループ全体のデータを集約するとともに、ユーザー部門や事業会社が構築・利用するアプリケーションとの連携を図りながらデータマネジメント基盤の活用を広げている。
一方でデータを活用するための人材を育成する必要がある。同社は4年前からデジタルプロフェッショナル人材を現場と一体となって育成しており、同社は全社員向けに「デジタル人材4万人プログラム」をeラーニングで実施し、7カ国語でコンテンツを提供する。
学習の成果は資格情報をデジタル証明・認証する仕組み「オープンバッジ」を用いて評価しており、レベル1からレベル3を全社員に取得させることを目標としている。2022年3月現在で約2万3,500名がレベル1~レベル2を取得済みだという。
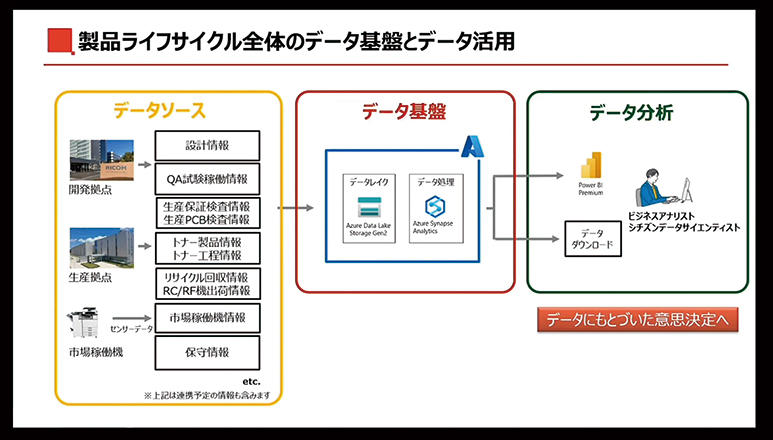
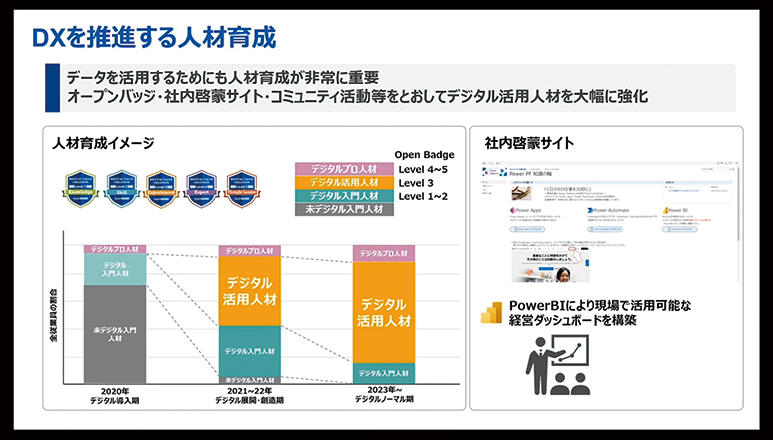
※ユースケースの画像は2022 年3 月15 日開催の記者説明会にて使用された投影資料の画面キャプチャーを許可を得て掲載しました。